Farrell works cooperatively in relationship with the design team to achieve the defined and common goal of foundation support for the owner’s building assets.
At Farrell, we approach the project with a high awareness to the shared goals of our customers; be it the owner, the engineer, or the contractor. We partner with the project team to provide the best foundation solution that fits the owner’s overall project goal.
As owners look to save money, engineers look to address poor soil conditions, and contractors look to expedite the schedule, Farrell’s experienced engineers and contractors are here to collaborate to assure your project will Go Vertical with Confidence!®
Farrell’s collaborative process is comprised of four steps. Click on each to learn more:
Coming together is a beginning, staying together is progress, and working together is success.
Henry Ford
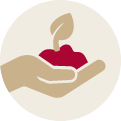
Farrell’s engineers will gather information about the soil conditions, foundation loading, and project constraints (environmental and physical). Farrell will perform risk assessment and make a qualified recommendation for the best foundation solution.
Farrell prepares Feasibility Letters with rough order of magnitude cost estimates (ROMs) to assist engineers, contractors, and owners in the decision process. Our goal is to provide you with a complete assessment of what is feasible at your site.
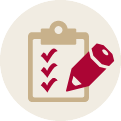
Farrell serves our customers with design and estimating services that bring value to their projects. With over 25 years of experience, Farrell has knowledge of the soil conditions and building code requirements to design the best and most reliable foundation solution. Get a BID now >
Design Assistance
Farrell collaborates with construction managers, contractors, engineers, developers, and owners to deliver proven foundation solutions on public, private, large, and small projects. Farrell’s goal in the design process is to minimize risk and offer a cost-effective solution. The project team can count on Farrell’s commitment to the success of the project.
Cost & Schedule Estimating
Cost estimating starts with the soil boring logs and a foundation plan. Schedule durations are estimated based on Farrell’s construction experience. Our estimators use the most current project data including soil, load, and layout conditions to provide cost estimates. Estimates are provided as required at the Schematic (ROM), Design Development (BUDGET), and Construction drawings (BID) phases of a project.
Farrell works with the GC to refine schedules and often provides schedule saving options including extended work hours and multiple crews.
Value Engineering – VE
Farrell has helped save millions of dollars on projects that were designed with expensive foundations. Farrell will evaluate your foundation plan and project requirements to VE a cost effective solution that will save money on your project.
3D Design
Farrell uses the latest, state-of-the art software and communication tools for the design team coordination. Farrell uses AutoCAD 3D and Revit to coordinate site plans and underground 3D models, Plaxis 3D for complex modelling, and many more.
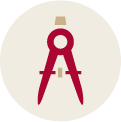
Contract Documents approved by these jurisdictions:
- DSA – Division of State Architect
- OSHPD – Office of Statewide Planning and Development
- CALTRANS – California Department of Transportation
- BART – Bay Area Rapid Transit
- NAVFAC – U.S. Navy Facility Command
- US COAST GUARD
- CSU – California State University System
- UC – University of California System
- County of Los Angeles
- Cities and Counties across California
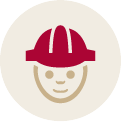
Construction
Once the preconstruction and design work is complete, Farrell delivers a full scope of construction services. Farrell will mobilize the appropriate equipment, construction crews, and subcontractors to layout and install ground improvement and deep foundations. Farrell’s engineers work proactively with the construction crew and interact daily during production to ensure the project stays on schedule and in budget. Farrell knows how important quality control is to the success of the project and has a structured approach to assure your project will Go Vertical with Confidence!®
Safety
Farrell’s safety program consists of the Injury and Illness Prevention Program, Site Safety Reviews, Jobsite Safety Plan, Activity Hazard Analysis, and Code of Safe Practices. These policy documents are trained on the first week of hire and regularly reviewed and discussed by all of Farrell’s employees. Company wide safety refreshers are held multiple times per year to go over new OSHA and California Safety rules and regulations.
Daily Safety Tailgate Meetings are conducted before each shift starts as well as weekly “topic specific” safety meetings every Monday morning. The Monday topic specific safety meetings minutes are provided to the General Contractor for their records.
Quality Control
- Quality Control Log: Each pile, column or compaction point has a unique QC number and specific depth, volume, and work data that is documented as each element is constructed and finished.
- Daily Construction Log: Farrell’s Superintendents prepare Daily Construction Logs (DCL) showing the total work completed that day, the QC number for each element from the Quality Control Log, and any changes made that day.
- Production Summary: Farrell prepares a construction schedule that is put into a Production Summary Worksheet and is reviewed daily by the Project Administrator based on the DCL. This ensures a regular review and conversation between the Farrell’s site Superintendent and Project Manager on schedule progress.
- Production Summary Worksheet: The Project Manager and the Project Administrator review the productivity data regularly to ensure that the project is on schedule. If production is not meeting planned schedule, the Project Manager will meet with the Superintendent to adjust production by extending work hours/days or adding additional crew to return to the planned schedule.
- Final Overview of QC Logs: When production is completed, the Quality Control Logs are returned to the Farrell office and the data is tabulated and reviewed by the Project Manager to ensure that all work was installed.
- Job Closure and As-Built Drawings: Once all of the project production information has been gathered, tabulated and reviewed, the Project Administrator and the Project Manager create the Job Closure Summary and As-Built Plans for the project. These documents will show what was installed and any changes that were made because of changed site conditions or changed work scope.
You can count on Farrell’s professional attention to construction, safety, and quality control to make your projectGo Vertical with Confidence!®